Great American Packaging expands automation, efficiency and capacity
Investment in a flexo press
In today’s flexible packaging market, there are two main drivers influencing brands and their customers: The demands for both sustainability and more sophisticated colourful branding.
Sustainability is a key trend, especially for manufacturers of food and retail products. New mandates from government and major retailers are driving the demand for cost-effective eco-friendly alternatives to non-recyclable films, even where highly colourful artwork is involved.
It is in this environment that Great American Packaging, as a manufacturer of custom-printed flexible packaging, is being asked to extrude, print and convert top-notch branded products in a wide range of styles and sizes.
To meet the ever-increasing consumer demand, Great American Packaging recently purchased a new Koenig & Bauer Flexotecnica Evo XD eight-colour press. “We are really excited about the opportunities which the new press has brought,” says GAP president Bruce Carter. “The new capabilities and increased performance are keys to success. The new press gives us the tools and resources to grow into new markets. It is bringing us greater efficiency and productivity through increased printing widths, faster printing speeds, quicker changeovers, better quality control and process capabilities. This competitive advantage allows us to produce recyclable multilayer pouches and films with sophisticated artwork in a cost-effective way.”
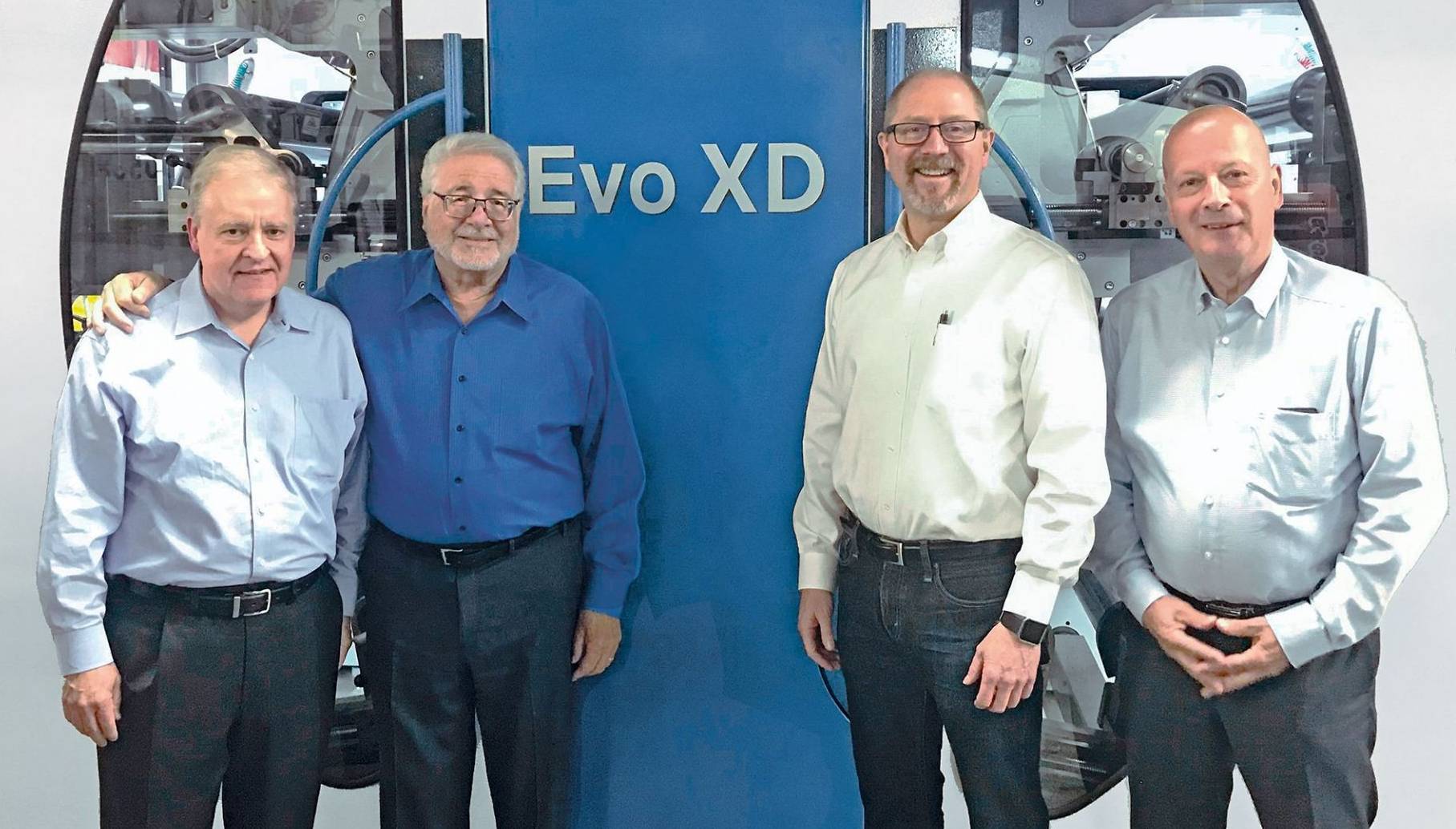
Great American Packaging was pleased to welcome top-ranking executives from Koenig & Bauer
Flexotecnica to its headquarters in Los Angeles (l-r): Mark Hischar, president and CEO of Koenig & Bauer (US); Greg Gurewitz, CEO of Great American Packaging; Bruce Carter, president of Great American Packaging; Dr. Peter Lechner, CEO of Koenig & Bauer Flexotecnica
The eight-colour Evo XD is the main workhorse press for Great American Packaging. It extends the six-colour custom-printed products currently being produced to eight colours, as well as enabling the creation of multi-colour images in both process and spot colours to meet the specific needs of customers and the growing demand for sophisticated images and branding.
The press operators, furthermore, are delighted with the high level of automation, which includes optical error detection, automated viscosity control, automatic wash-up, automatic impression setting, servo control, the saving of all important job settings, automatic splicing and automatic tension control.
“When we compared the major flexographic press manufacturers, we found that Koenig & Bauer offers the right combination of build quality, technology, sales support, value and commitment to the US market, making it the ideal choice for our company,” says CEO Greg Gurewitz. “They offered superior reliability paired with a sleek and functional design. We were especially won over by the cutting-edge support systems for maintenance and repair. Interactive glasses allow our print operators to connect with a Koenig & Bauer Flexotecnica technician and give them a real-time view of our equipment.”
Eric Frank